Is Used Warehouse Racking Worth It? Pros, Pitfalls, and Practical Advice
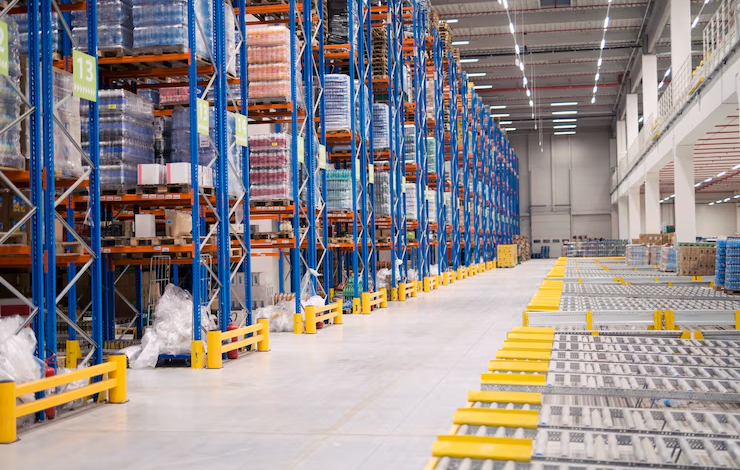
There’s always pressure to cut costs in every enterprise. Every warehouse manager has felt it—balancing space, safety, and budget while trying to keep operations from stalling. At some point, someone suggests buying used racks instead of new ones. Sounds simple enough. Just buy what you need, bolt it down, and save a good chunk of change.
That’s where used warehouse racking usually enters the conversation. It’s not a new idea. Businesses have been doing it for years. But is it smart? Depends who you ask.
Some swear by it. Others won’t go near it. So what’s really going on?
Why Used Racking Even Considered
It almost always comes down to budget. New racking systems can be expensive—not just the material, but the installation, the permits, the extras. Used racks look like an obvious shortcut.
- They’re cheaper—often by 30 to 50 percent.
- You might find them locally and avoid long lead times.
- And if you’re starting small or testing a layout, why spend more than you have to?
That’s the logic, anyway. And in theory, it makes sense.
But warehouses aren’t theoretical. They’re real places with moving machinery, shifting loads, and real people walking underneath these structures every day. That’s where doubts start creeping in.
See also: AI Image Generator: Transforming Creativity with Technology
So… What’s the Risk?
Well, for starters, you don’t know what those racks went through before landing in your facility. Were they overloaded? Dropped? Repaired badly? No one likes to admit it, but damage gets ignored sometimes. Corners get bent. Bolts go missing. You’d be surprised what people will sell when a warehouse shuts down.
Structural wear isn’t always visible
A rack can look fine and still be weakened. Especially if it’s been hit by a forklift—more common than people think.
Missing certifications or labels
Without labels showing load capacity, you’re guessing. Guessing under 500 kg of stock is not ideal.
Mix-and-match problems
New beams with old uprights, different bolt patterns, missing spacers… the parts might not fit right, but you won’t know until you’re halfway through assembly.
Compliance issues
Codes vary by region. A rack built to one standard might not legally meet requirements elsewhere. And retrofitting? That adds time and cost.
And of course, there’s the safety factor. Used isn’t bad by default, but it adds questions. The fewer answers you get, the higher the risk.
When It Might Be a Smart Call
That said, not every warehouse is the same. Some can get away with using older systems, and it works out just fine. Maybe you’re:
- Expanding a temporary section
- Testing layout changes before investing long-term
- Working with lightweight, non-critical loads
- Replacing parts in an older system you already have
In those cases, second-hand racking might not be a compromise—it could be a practical move.
But it really comes down to how much uncertainty you’re willing to accept.
Things to Watch Closely
Before committing, try to inspect the racking in person. Photos can hide a lot. If that’s not possible, ask particular questions.
- Were they used indoors or outdoors?
- Any damage from forklifts or corrosion?
- Can you match the system to a known brand or model?
- Are original load ratings available?
And look carefully at welds, footplates, beams, and braces. If you spot rust in joints or tiny cracks near welds, that’s a red flag. Surface rust might not matter, but internal damage definitely does.
Also, be ready to measure everything. Even a 2-inch height mismatch can mess with clearance and pallet access. Doesn’t sound like much until a forklift gets stuck trying to lift.
A Word About Liability
This part gets overlooked. If a rack collapses—even from undetected damage—you’re still liable. Insurance might cover some of it, but regulatory agencies will want answers. And if someone gets hurt, things can spiral fast.
Used equipment doesn’t automatically mean unsafe. But if you cut corners on inspection or ignore warning signs, the risks proliferate. That’s just the reality of working in environments where weight and gravity don’t forgive mistakes.
Is There a Middle Ground?
Yes, sometimes. Some suppliers refurbish used racking professionally. They clean, inspect, replace damaged parts, and recertify everything. It costs more than raw second-hand racks, but it also removes much of the guesswork.
Another option: buy new for critical areas (like high-load zones) and used for light-duty sections. It’s not a perfect solution, but it spreads the budget more thoughtfully.
And occasionally, buying used just doesn’t work. Especially when timing, layout, or compatibility throw too many problems your way. In those cases, biting the bullet and buying new can save weeks of headaches later.
It’s Not About “New” or “Used.” It’s About Fit.
At the end of the day, the label doesn’t matter. What matters is whether the rack suits your space, your load, and your team. If it’s safe, fits well, and doesn’t come with hidden surprises, it could be worth it.
But if things feel rushed or unclear, pause. Ask more questions. Take another look.
Because when it comes to warehouse racking, it’s not just storage. Its structure. It’s safe. And sometimes, it’s the thing standing between daily routine and a horrible day.