Corrosion Champions: Understanding the Resistance of 304 Stainless Steel
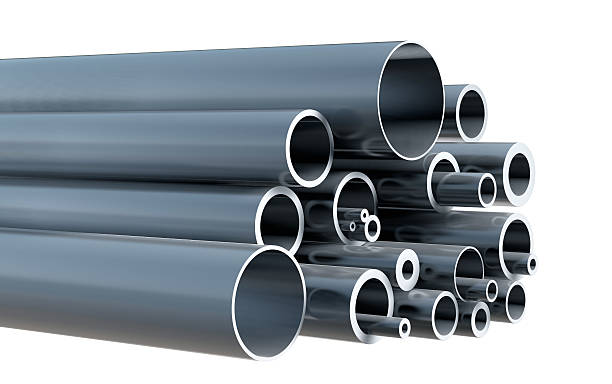
Equipment failure costs more than just replacement parts in the overall picture of a manufacturing unit. When corrosion strikes critical systems, production stops, deadlines slip, and profits disappear. Perhaps that’s why smart engineers choose materials that fight back against corrosion from day one. The science behind corrosion resistance reveals why some metals survive while others surrender to rust and decay.
The remarkable performance of 304 stainless steel tubes stems from its unique chemical composition and protective mechanisms. This austenitic grade contains chromium and nickel in precise ratios that create an invisible shield against environmental attack. When exposed to oxygen, the chromium forms a passive layer that self-repairs and regenerates. This natural protection explains why 304 grade stainless steel remains the preferred choice for demanding applications.
The Science of Passive Protection
Chromium Oxide Layer Formation: The moment 304 stainless steel contacts oxygen, something remarkable happens. Chromium atoms at the surface combine with oxygen to form an ultra-thin chromium oxide layer. This passive film measures just nanometers thick yet provides incredible protection against rust formation. The layer adheres strongly to the base metal and resists penetration by most corrosive agents.
Self-Healing Properties: Damage to the passive layer triggers an automatic repair process. Fresh chromium migrates to the surface and reacts with available oxygen. This regeneration happens within seconds under normal atmospheric conditions. The self-healing capability means minor scratches or surface damage don’t compromise long-term corrosion resistance.
Chemical Composition Benefits: The 18-20% chromium content provides the foundation for passive layer formation. Nickel additions improve overall corrosion resistance and enhance the stability of the austenitic structure. Carbon content stays below 0.08% to minimize carbide precipitation that could weaken corrosion resistance. Silicon and manganese additions support deoxidation and improve hot working properties.
See also: Decoding Device Costs: Understanding What Influences Laptop Pricing
Environmental Performance Characteristics
Atmospheric Corrosion Resistance: Standard atmospheric conditions pose little threat to 304 stainless steel. The material withstands rain, humidity, and temperature fluctuations without visible corrosion. Urban environments with moderate pollution levels rarely cause problems. Even coastal areas with salt spray show minimal impact when proper maintenance practices are followed.
Organic Acid Compatibility: Many organic acids that destroy carbon steel have minimal effect on 304 stainless steel. Acetic acid, citric acid, and formic acid in moderate concentrations rarely cause significant corrosion. The passive layer remains stable in these environments. Food processing applications benefit from this resistance since natural acids from fruits and vegetables don’t compromise the material.
Temperature Considerations: Elevated temperatures can affect corrosion resistance in specific environments. The passive layer remains stable up to about 1600°F in oxidizing conditions. Higher temperatures may require grade upgrades or special considerations. Thermal cycling generally doesn’t harm the protective characteristics if proper design practices are followed.
Industry Applications and Benefits
Food Processing Excellence: Hygiene requirements in food processing demand materials that resist corrosion while maintaining cleanliness. 304 stainless steel meets FDA requirements for food contact surfaces. The smooth surface finish prevents bacterial growth and allows thorough cleaning. Acidic foods like tomatoes and citrus products don’t compromise the material’s integrity over time.
Pharmaceutical Manufacturing Standards: Drug manufacturing requires materials that won’t contaminate products or degrade under cleaning protocols. 304 stainless steel withstands repeated sterilization cycles without degradation. Chemical cleaning agents used in pharmaceutical facilities rarely affect the passive layer. The material’s purity meets stringent pharmaceutical industry standards.
Chemical Processing Applications: Many chemical processes involve corrosive substances that would destroy ordinary metals. 304 stainless steel handles numerous chemicals safely when properly specified. Process equipment manufacturers rely on its predictable performance. The material’s resistance to stress corrosion cracking adds another layer of protection in demanding applications.
Limitations and Considerations
Chloride Sensitivity Concerns: Chloride ions present the greatest threat to 304 stainless steel’s corrosion resistance. Saltwater environments can cause pitting and crevice corrosion. Swimming pool chemicals and de-icing salts create similar risks. Understanding these limitations helps engineers select appropriate grades for specific applications.
Stress Corrosion Cracking Risks: The combination of tensile stress and chloride exposure can lead to stress corrosion cracking. This phenomenon occurs most commonly in warm chloride environments. Proper design practices and stress relief treatments minimize these risks. Alternative grades like 316 offer better chloride resistance when needed.
Key factors that influence 304 stainless steel performance include:
- Temperature exposure levels and cycling patterns
- Chloride concentration and contact duration
- pH levels of process media or cleaning solutions
- Presence of oxidizing or reducing conditions
- Mechanical stress levels and distribution patterns
Maintenance and Longevity Factors
Surface Condition Impact: The condition of the surface finish affects corrosion resistance significantly. Smooth, clean surfaces provide better protection than rough or contaminated ones. Regular cleaning removes deposits that might interfere with passive layer formation. Proper surface preparation during fabrication sets the foundation for long-term performance.
Cleaning Protocol Importance: Appropriate cleaning methods preserve the passive layer while removing contaminants. Mild alkaline cleaners work well for routine maintenance. Acidic cleaning solutions can restore the passive layer after contamination. Avoiding chlorinated cleaners prevents unnecessary chloride exposure that could initiate corrosion.
Conclusion
The corrosion resistance of 304 grade stainless steel represents a perfect balance of chemistry, physics, and engineering. Its passive chromium oxide layer provides reliable protection across numerous applications while maintaining cost-effectiveness. Understanding these protective mechanisms helps engineers make informed material selections that prevent costly failures. Don’t let corrosion compromise your next project – evaluate whether 304 stainless steel’s proven resistance matches your application requirements and contact qualified suppliers for specification guidance.